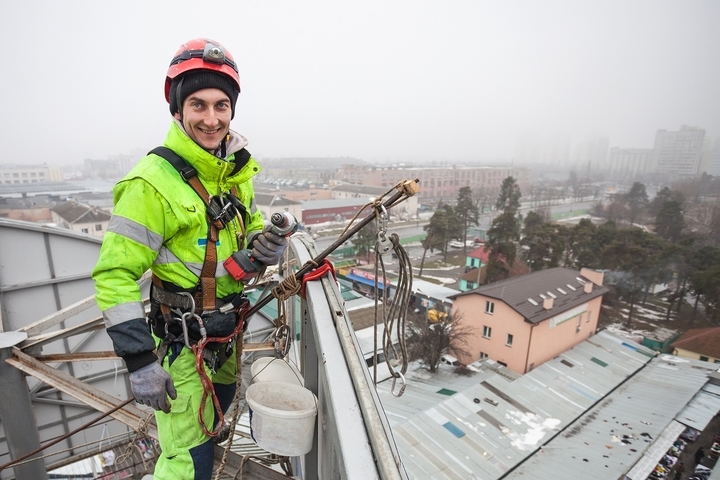
Whenever you or your team is working at heights, safety precautions become a necessity. A lot of injuries and work-related deaths can be prevented with some due diligence. This article looks at five basic tips your team needs to internalize when working at heights.
1. Assess The Work Environment Before Making The Climb
Start by making a list of potential risks such as how high you have to climb, if there’s potential for falling objects and what type of equipment you need to complete the job. Assessing the work area beforehand can sometimes reveal options where there’s no need for you to make the climb.
Anytime an accident occurs, or if there is a change in personnel, you need to re-evaluate the risks. Getting the opinions of people who are familiar with the worksite will help you identify risks that you can only see with experience. After you’re done compiling the risks, make a checklist to ensure safety protocols are followed.
2. Don’t Overestimate The Safety Of Your Ladder
A lot of people (especially untrained people) often overestimate the safety of their ladders. Whenever you work with a ladder, you need to ensure basic safety conditions are met. Your ladder should always be on level ground, away from wet, muddy or icy surfaces. Even if you’re used to working with a ladder, you should check that the braces are locked down before you put your full body weight on it; otherwise, the ladder can buckle.
3. Take Precautions When Working With Scaffoldings
Similar to working with a ladder, you need to make sure your scaffolding is safe before you start using it. Make sure when you calculate the maximum load capacity that you include all the equipment you need to complete the job. A safe scaffolding needs to have a minimum of three guardrails (including the toe board) on each side of the platform.
4. Make Sure You’re Using The Proper Fall Arrest Systems
It’s not enough to just use a fall arrest system; you need to ensure that it is appropriate for the job. All full body harnesses meet ANSI standards, but there are slight differences that you usually see reflected in the price. Depending on your job, you may need a harness made of fireproof material or one that has extra D-rings.
Another issue to consider when searching for fall arrest anchors is to try and buy comfortable equipment for your staff. Of course, safety trumps comfort, however, it’s easier to get a high level of performance from your team if they feel comfortable. Remember that harnesses are NOT one-size-fits-all. Attempting to use the same harness for everyone can result in an easily avoidable accident.
5. Inspect Your Equipment Before Work Begins
Equipment is no good to you or your team if it isn’t inspected before work begins. You should have at minimum one person on your staff who understands how to recognize hazards in safety equipment and has the skills to correct it. Your team needs to know what to look for, what’s acceptable in safety equipment and what steps to take when they find a problem.
Another part of the pre-work inspection has to include understanding the fall distance. Safety equipment doesn’t do much good if your safety lines aren’t the appropriate length to stop a fall. Assessing the fall distance will allow you to choose the right type of fall arrest system for the project you’re working on.